Manual & Machine Assembly
Manual & Machine Assembly
Benefits of Hand Placement
-
Solder through-hole components without product delay
-
High accuracy of component placement, assembled to IPC-610 Standards
-
Does not depend on production line availability
-
Avoid defects which can occur when using semi-automatic equipment
Assembly in 24 hours
IPC certified assemblers
Single board assemblies
Configuration builds
Express delivery
We also offer machine
component placement
Surface Mount (SMD) Component Placement
- Dedicated high volume machines for fast turn-around
- Low to medium production builds
- Custom test equipment
- Competitive Pricing
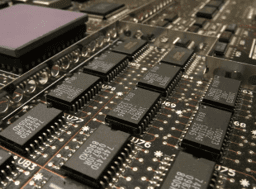
Electromechanical Assembly
We have the capability to design products and provide turnkey assemblies that incorporate mechanical, electrical, and electro-mechanical components. We can also run automated test suites to validate the quality of the produced products. This allows us to provide a complete solution to our customers, from design to delivery.
Flexible Assembly Services
Outsourcing your electromechanical assembly to Electronics4All, means high quality, efficient delivery, exceptional yield, and flexibility that is tailored for your needs.
Our team handles the entire supply chain including procurement of materials, assembly, quality testing, documentation, and delivery of the electromechanical assembly to our client.
We provide consistently high-quality assemblies that you can trust, enabling your team to focus on business expansion and sales. Our team will plan the manufacturing and assembly process, while not losing sight of both cost efficiency and quality.
Electronics4All is an ISO 9001:2015 certified company, which demonstrates our commitment to providing high quality services for our clients.
Our existing and expanding supply chain network of trusted partners enables us to commit to fast and efficient delivery. Even for the toughest quality and time requirements, we have a solution for that too.
Expertise.
We have the expertise necessary to design and assemble electromechanical products of the higher quality and complexity.
Quality.
Our Quality Management System, electronics and mechanical testing suites, and traceability, guarantee high yields for your products.
Flexibility.
Flexibility is critical for our clients' success. Our team handles multiple variations of product assemblies, known as configuration builds.
Custom Made.
We tailor our assembly service to our clients' needs. It's as simple as requesting a change, and our team is ready to make it a reality.
Wire Harness Assembly
E4A designs and manufactures customized wiring harnesses for a wide range of applications. Our experienced engineering team can deliver custom-made, multi-core, varying termination harnesses to solve any problem you may encounter.
There is an endless variety of cable harness configurations available. Electronics4All's experts can custom design and build your harness with any of the following inputs:
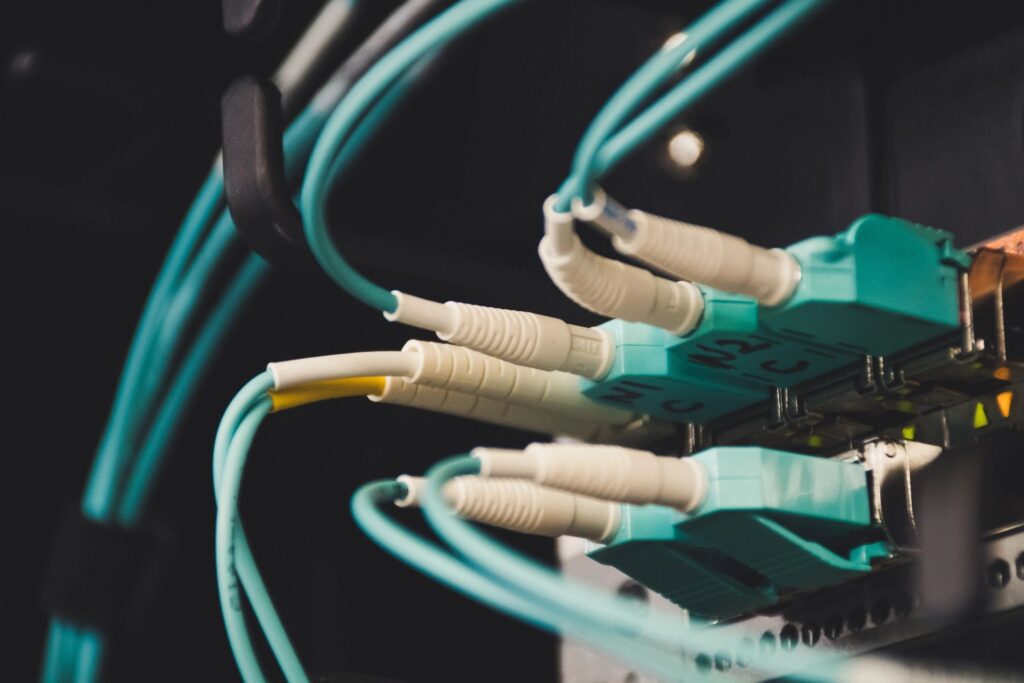
4 Main Steps in Wire Harness Assembly
Whether your wire harness has 5 wires or 100 wires, the assembly process typically follows the steps outlined below:
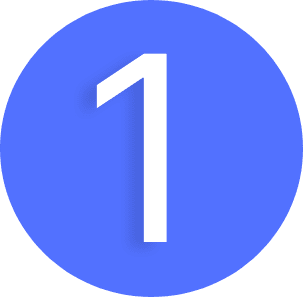
Wire Cutting and Labelling.
The wires are first cut to the desired length indicated on the design and labeled appropriately. Proper labeling is a critical step in this process.
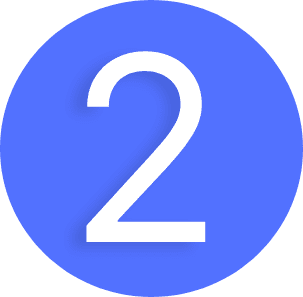
Wire Termination.
The end of each wire is stripped to expose the uninsulated conductor and fitted with the required connectors and terminals.
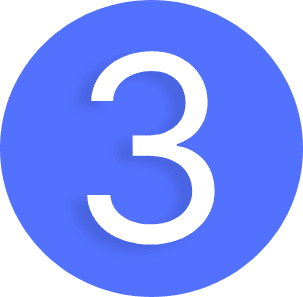
Wire Assembly.
Wires and components are assembled and bound together based on the specification outlined in the design.
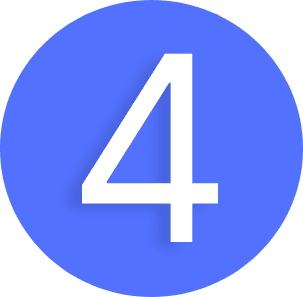
Wire Testing.
The harness is tested for electrical functionality. This testing is done with the aid of a pre-programmed test board that checks for faults in the completed harness.
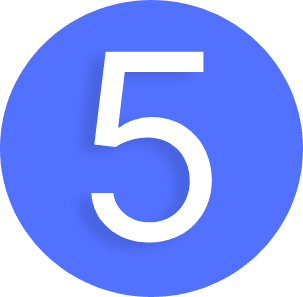
Embed Logo.
The final step of the assembly process is to embed tags with your company logo or add text to the wire harness for a professional look.